
SCARA THL-Series
SCARA THL-Series
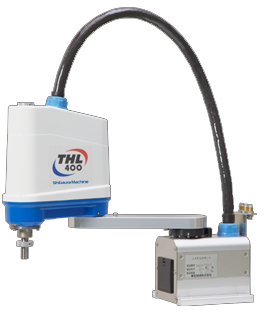
Shibaura Machine’s range of SCARA industrial robots is believed to be the widest in Europe. Ranging from the tiny TH180, ideal for use in high precision applications, to the impressive TH1200A, which finds a home in heavy duty pick and place applications, the entire series is easy to install, program and manage.
SCARA stands for Selective Compliant Assembly Robot Arm or Selective Compliant Articulated Robot Arm – the two acronyms are both common and are entirely interchangeable. This acronym is the key to understanding the advantages of a SCARA robot.
The first thing to recognise is the robot’s parallel-axis joint layout, which is compliant in the X-Y direction but rigid in the ‘Z’ direction, hence the term ‘Selective Compliant’. This offers enormous advantages in all sorts of primary and secondary packaging applications as well as a host of other pick and place functions. Secondly, the jointed, two-link arm layout is similar to a human arm, which is why the phrase ‘articulated’ forms part of the acronym. As a result, the robot can reach into confined areas and then fold back out of the way.
Shibaura Machines’ SCARA robots are available with a host of options, including ceiling mount, IP65, conveyor synchronisation and vision.
Standard specifications SCARA-THL-Series 300 - 700 |
|||||
|
THL300 |
THL400 |
THL500 |
THL600 |
THL700 |
No. of controlled axes |
4 |
||||
Arm length total, |
300 |
400 |
500 |
600 |
700 |
Working envelope |
|
||||
Axis 1 |
+/-125° |
||||
Axis 2 |
+/-145° |
||||
Axis 3 (z-Axis ) |
0 … 160 mm |
0 … 150 mm (optional 300 mm) |
|||
Axis 4 (z-Axis rotation) |
+/-360° |
||||
Maximum speed |
|||||
Axis 1 |
660 °/s |
450 °/s |
|||
Axis 2 |
660 °/s |
450 °/s |
|||
Axis 3 (z-Axis ) |
1120 mm/s |
2000 mm/s |
|||
Axis 4 (z-Axis rotation) |
1500 °/s |
1700 °/s |
|||
|
|||||
Composite |
5,1 m/s |
6,3 m/s |
6,3 m/s |
7,1 m/s |
7,9 m/s |
Standard cycle time (with 2kg load) |
0,48 s |
0,47 s |
0,45 s |
0,45 s |
0,5 s |
Maximum payload mass |
5 kg |
10 kg (Ratings 2kg) |
|||
Allowable moment of inertia |
0,05 kgm² |
0,2 kgm² |
|||
Positioning repeatability |
|||||
X, Y |
+/-0,01 mm |
||||
Z (Axis 3) |
+/-0,015 mm |
||||
Z-Axis rotation 4 |
+/-0,007° |
||||
|
|||||
Input / output signals for hand |
8 Inputs / 8 outputs |
||||
Pneumatic piping for hand |
Ø 4 x 3 pcs. |
Ø 6 x 3 pcs. |
|||
Position detecting system |
Absolute |
||||
Robot-controller cable |
3,5 m |
||||
Mass of robot body |
12 kg |
13 kg |
22 kg |
23 kg |
24 kg |
Standard specifications SCARA-THL-Series 800 - 1000 |
|||
|
TH800 |
THL900 |
THL1000 |
No. of controlled axes |
4 |
||
Arm length total, |
800 |
900 |
1000 |
Working envelope |
|||
Axis 1 |
+/-125° |
||
Axis 2 |
+/-145° |
||
Axis 3 (Z-axis) |
0 … 300 mm |
||
Axis 4 (Z-axis rotation) |
+/-360° |
||
Maximum speed |
|||
Axis 1 |
187,5 °/s |
||
Axis 2 |
217,5 °/s |
||
Axis 3 (Z-axis) |
2000 mm/s |
||
Axis 4 (Z-axis rotation) |
1700 °/s |
||
|
|||
Composite |
4,3 m/s |
4,6 m/s |
5,0 m/s |
Standard cycle time (with 2kg load) |
0,47 s |
0,48 s |
0,48 s |
Maximum payload mass |
10 kg (Ratings 2kg) |
||
Allowable moment of inertia |
0,2 kgm² |
||
Positioning repeatability |
|||
X, Y |
+/-0,02 mm |
||
Z (axis 3) |
+/-0,015 mm |
||
Z-axis rotation 4 |
+/-0,007° |
||
|
|||
Input / output signals for hand |
8 inputs / 8 outputs |
||
Pneumatic piping for hand |
Ø 6 x 3 pcs. |
||
Position detecting system |
Absolute |
||
Robot-controller cable |
3,5 m |
||
Mass of robot body |
32 kg |
34 kg |
36 kg |
Controller |
||
TS3000E |
TS3100E |
|
Number of axis |
Standard 4 axis, maximum 5 axis |
Maximum 8 axis simultaneous control |
Operation mode |
PTP, CP (linear, circular), Short cut, Arch motion |
|
Position detecting system |
Absolute -Encoders |
|
Storage capacity |
Total: 12800 points + 25600 steps 1 program: 2000 points + 3000 steps |
Total: 12800 points + 25600 steps 1 program: 2000 points + 3000 steps |
No. of programs |
Max. 256 (247 user files + 9 system files) |
|
Programming language |
SCOL (Symbolic Code Language, similar to BASIC) |
|
Teaching unit (option) |
Teach Pendant TP1000, 5-meter cable, (Program can be written on PC) |
|
External I/O |
32 inputs / 32 outputs |
32 inputs / 32 outputs |
Hand control signal |
8 inputs / 8 outputs |
8 inputs / 8 outputs |
External operation signal |
Inputs: Cycle operation start,stop,reset,etc Outputs: Servo-On status, emergency stop, ready for operation, malfunction alarm, etc |
|
Serial communication port |
2 x RS-232C, 1 x Ethernet |
2 x RS-232C, 1 x Ethernet |
Power supply |
Single phase 200/240 V AC, 50/60 Hz, 2,3 kVA |
Single phase 200/250 V AC, 50/60 Hz, 4,4 kVA |
Dimension (WxHxD), Mass |
290 x 230 x 298 [mm], 13 kg |
420 x 230 x 298 [mm], 17 kg |
Other functions |
Torque control,Interruptive functions, self-diagnosis, I/O control and communications during motion, Coordinate calculations, Built-in PLC, etc |
|
Certification |
Safety relais box TS3SFB, according to safety category 3 corresponding to ISO10218-1:2011 and ISO13849-1:2008 |
|
Options |
I/O extention, I/O cable, Field-Network (DeviceNet®, CC-Link®, ProfiBus®) |
EXHIBITION
SAVE THE DATE
Hamburg, June 03-04, 2025
Kalkar, September 23-24, 2025
Nuremberg, November 25–27, 2025
SOCIAL MEDIA
Follow us on